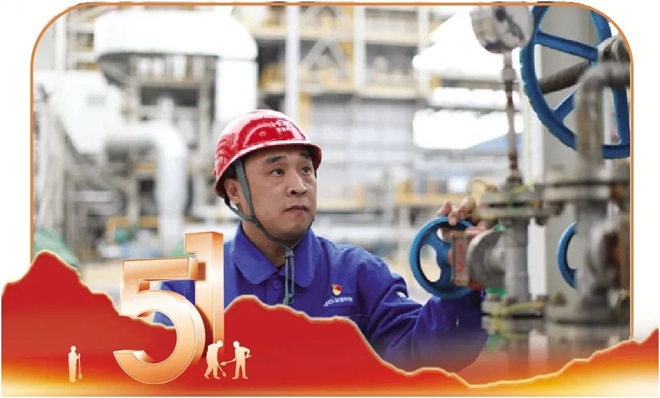
圖為李利杰正在檢查設備。(張宣科技 供圖)
走進位于河北張家口的河鋼集團張宣科技,120米高的氫基豎爐巍然矗立。生產綠色汽車板材料的主要原料氫基直接還原鐵,就“誕生”于這座全球首例120萬噸氫冶金示范工程中。在這一示范意義重大、減排效果顯著、產品綠色經濟的工程背后,有大量技術精湛、潛心創新、拼搏實干的鋼鐵人,全國勞動模范,河鋼集團張宣科技氫冶金公司氫冶金作業區作業長、高級工程師李利杰正是其中一員。
從2006年進入張宣科技到2022年加入張宣科技氫冶金公司,再到如今,奮斗在一線的19個年頭里,李利杰從一名普通職工做起,跨越傳統“碳冶金”“氫冶金”兩套工藝界限,始終不曾衰減的是對鋼鐵冶金的熱愛。
在全球首例120萬噸焦爐煤氣直接還原氫冶金示范工程一期安全順利連續生產、各項技術和經濟指標保持穩定后,氫冶金的先行優勢得以體現。據統計,氫基DRI(直接還原鐵)金屬化率達到94%,與同等生產規模的長流程工藝相比,每年可減少二氧化碳排放量80萬噸。
以氫代碳是鋼鐵冶煉技術的重大創新。逐步擴大先行優勢,用中國標準引領鋼鐵行業發展成為李利杰的新愿望。
氫冶金存在許多無人觸及的未知領域,在探索過程中,會出現不少難以預料的問題。作為產線負責人,李利杰不是在主控室跟氫冶金外方團隊關注各項運行參數,就是在密布著管道與儀表的作業現場研究改進設備。200頁的氫冶金技術操作規程里,詳細注明了7個大項、上百個小項的技術規定,這都是李利杰帶著團隊一點一點試出來的。
打破外方專家“逢停機必排料”的理念束縛,創新實施“氫基豎爐不排料、系統保壓操作”,在確保DRI百分之百合格的同時,大大加快了檢修后復產進程,每次檢修復產可節省費用173萬元,就連開機操作時間也從原來的8個小時以上縮短至3個小時以內……突出成效的背后,是李利杰“三年不窺園”的恒心和決心。
李利杰在氫冶金材料備件國產化替代攻關中,累計實施工藝優化改造112項,完成國產化替代122項,“全球首例”設備國產化率超過70%。開發“錐部氣體分配控制技術”,摸索出“金屬化率—產量—頂溫”最佳匹配參數,能量利用率大幅提升。
李利杰緊緊抓住氫冶金示范工程品牌效應帶來的技術交流機會,密切關注氫冶金技術發展與研究前沿動態,積極承擔科研課題研究,加強低碳冶煉技術的學習和研發應用。截至目前,他和團隊已申請氫冶金領域相關專利64項,獲得授權27項,申報《直接還原工廠CO2脫除技術規范》氫冶金技術相關標準11項,其中《煉鋼用氫基豎爐直接還原鐵》《氫基豎爐直接還原用球團》2項行業標準已被工信部批準立項。
2024年9月份,李利杰帶領團隊在國際上首次實現“綠氫”氫冶金工業化生產,直接還原鐵合格率達到100%,成功驗證了“綠電—綠氫—綠鋼”生產的技術可行性,助力企業邁出了探索全綠氫近零碳氫冶金技術的重要一步,登上2024年度“行業綠色低碳引領十大事件”榜單。
“將個人的專業技術能力和國家戰略需求相匹配,將自身的成長與企業的發展愿景相結合,我覺得這就是一個企業員工的最大價值。”李利杰說。(王楊)
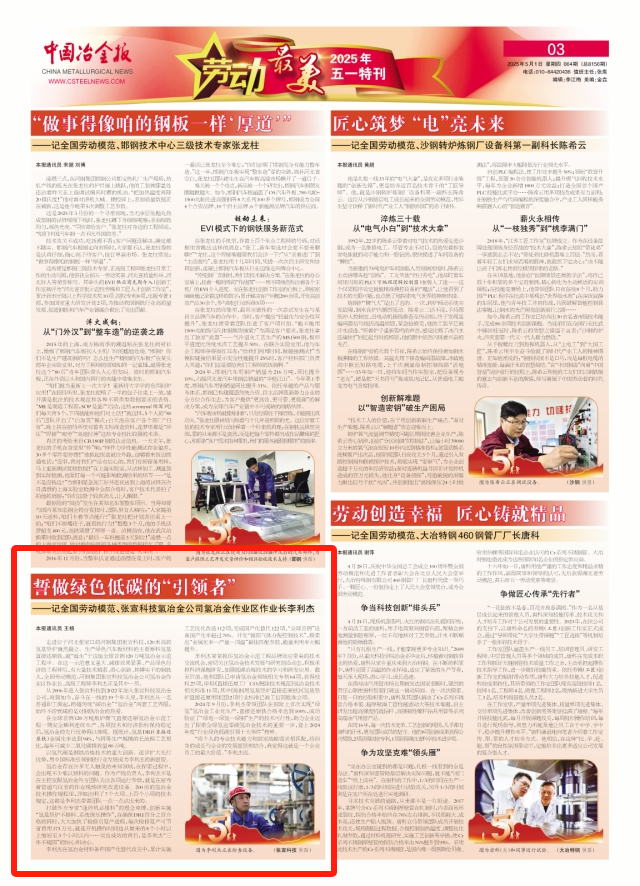